Söödagraanulimasina granuleerimisprotsessi ajal on üksikud söödagraanulid või erineva värviga üksikud söödagraanulid, mida tavaliselt tuntakse "lillesöödana". Selline olukord on veesööda tootmisel tavaline, mis väljendub peamiselt selles, et rõngasvormist väljapressitud üksikute osakeste värvus on tumedam või heledam kui teistel tavalistel osakestel või üksikute osakeste pinnavärvus on ebaühtlane, mõjutades seeläbi kogu söödapartii välimust.
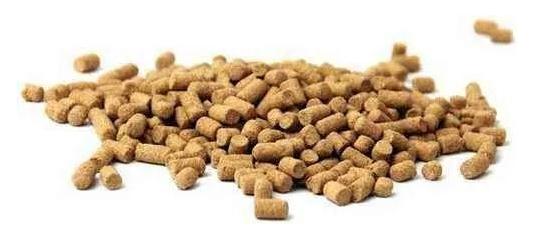
Selle nähtuse peamised põhjused on järgmised:
a)Söödatooraine koostis on liiga keeruline, liiga palju toorainetüüpe, ebaühtlane segunemine ja ebaühtlane pulbri niiskusesisaldus enne söödaosakeste töötlemist.
b)Granuleerimiseks kasutatavate toorainete niiskusesisaldus on ebaühtlane. Veetoidu tootmisprotsessis on sageli vaja lisada segistisse väike kogus vett, et kompenseerida vee kadu tooraines pärast ülipeent purustamist. Pärast segamist saadetakse see seejärel karastamiseks konditsioneerisse. Mõned söödatootjad kasutavad sööda valmistamiseks liiga lihtsat protsessi – panevad segu jaoks vajalikud materjalid otse segistisse ja lisavad piisavalt vett, selle asemel, et viia läbi üksikasjalik ja aeglane lisamisprotsess vastavalt professionaalsetele nõuetele. Seetõttu on neil raske tagada sööda koostisosade tasakaalustatud jaotust vees lahustuvuse osas. Kui kasutame neid segatud koostisosi konditsioneerimiseks, avastame, et palsami efektiivsuse tõttu ei saa niiskusesisaldust kiiresti ühtlaselt hajutada. Seetõttu on töödeldud söödatoodete küpsus auruga toimel erinevates osades väga erinev ja värvide hierarhia pärast granuleerimist ei muutu piisavalt selgeks.
c)Granuleerimiskastis on korduva granuleerimisega taaskasutatud materjale. Granuleerimisjärgset granuleeritud materjali saab valmistooteks muuta alles pärast jahutamist ja sõelumist. Sõelutud peenpulber või väikeste osakestega materjal siseneb sageli uuesti granuleerimiseks tootmisprotsessi, tavaliselt segistis või ootab granuleerimissilo. Kuna seda tüüpi tagastusmaterjal on konditsioneeritud ja granuleeritud, võib see pärast konditsioneerimist ebaühtlaselt segada teiste abimaterjalidega või segada tagasipöördumismasina väikeste osakestega materjalidega teatud söödasegude jaoks mõnikord "lillematerjali".
d)Rõngasvormi ava siseseina siledus on ebaühtlane. Matriitsi augu ebaühtlase pinnaviimistluse tõttu on objektil ekstrusiooni ajal kogetav takistus ja ekstrusioonirõhk erinev, mille tulemuseks on ebaühtlased värvimuutused. Lisaks on mõnel rõngasvormil väikeste aukude seintel pursked, mis võivad ekstrusiooni käigus kriimustada osakeste pinda, mille tulemuseks on üksikute osakeste pinnavärvid.
Eespool loetletud "lillematerjalide" tootmise nelja põhjuse täiustamismeetodid on juba väga selged, peamiselt kontrollides iga komponendi segamise ühtlust valemis ja lisatud vee segamise ühtlust; Karastamise ja karastamise tõhususe parandamine võib vähendada värvimuutusi; Kontrollige tagastusmasina materjali. Valemite puhul, mis kipuvad tootma "lillematerjali", proovige tagastusmasina materjali mitte otse granuleerida. Tagastusmasina materjal tuleks segada toorainega ja uuesti purustada; Matriitsi aukude sileduse kontrollimiseks kasutage kvaliteetseid rõngasstantse ja vajadusel lihvige rõngasvormi augud enne kasutamist.
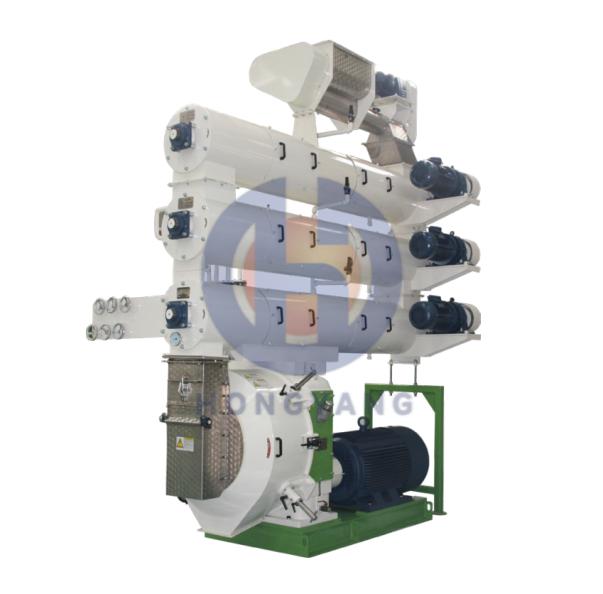
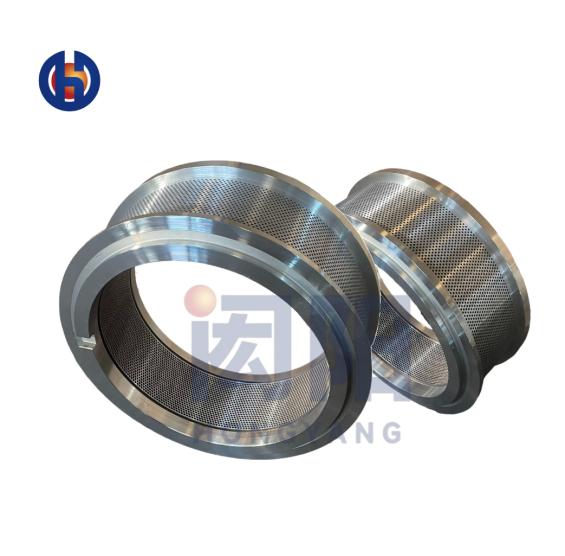
Soovitatav on konfigureerida kahekihiline kaheteljeline diferentsiaalpalsam ja kahekihiline pikendatud särgiga konditsioneer, mille karastusaeg on kuni 60-120 sekundit ja kustutustemperatuur üle 100 ℃. Kustutus on ühtlane ja jõudlus on suurepärane. Mitmepunktilise õhu sisselaskeava kasutamine suurendab oluliselt materjali ja auru ristlõikepindala, parandades seeläbi materjali küpsust ning parandades karastus- ja karastusefekti; Digitaalne näidikupaneel ja temperatuuriandur suudavad kuvada konditsioneeri temperatuuri, muutes kasutajatel seda igal ajal hõlpsalt kontrollitavaks.
Tehnilise toe kontaktandmed:
Whatsapp: +8618912316448
E-post:hongyangringdie@outlook.com
Postitusaeg: 26. juuli 2023